Energy Efficiency in Life Sciences Facilities: Challenges and Solutions
Energy management within life sciences facilities requires maintaining precise environmental controls, which are critical for both regulatory compliance and operational success. These facilities face unique energy challenges, but innovative solutions are emerging to enhance energy efficiency without compromising precision or reliability. The latest advancements and strategies are setting new standards in energy management for the life sciences sector, offering promising ways to meet these exacting demands.
Life sciences facilities, encompassing pharmaceutical manufacturing, biotechnology research, and clinical testing laboratories, require exceptionally controlled environments. Stringent temperature, humidity, and air purity levels are non-negotiable to ensure the validity of experimental results and the integrity of product development. This high level of control, however, results in substantial energy consumption making energy efficiency a significant challenge.
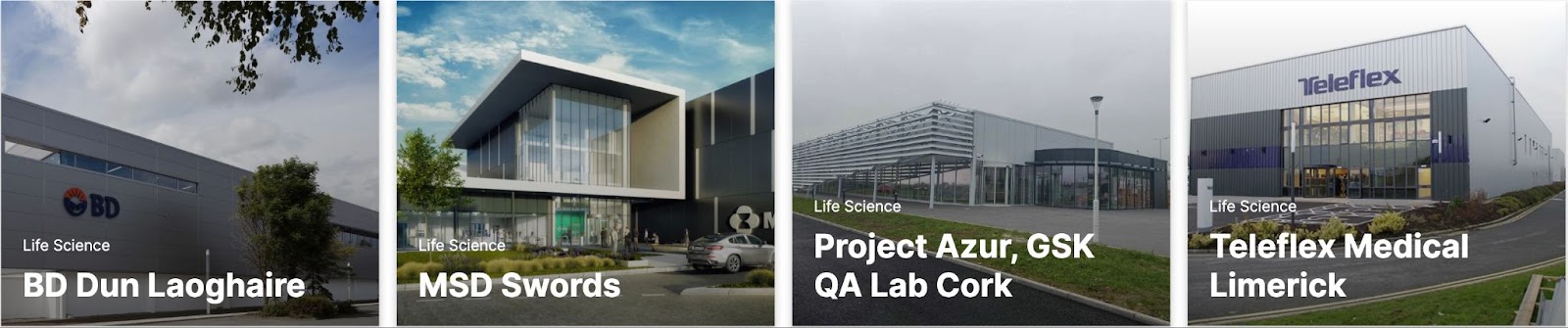
1. Advanced HVAC Systems:
One of the largest energy consumers in any life sciences facility is the Heating, Ventilation, and Air Conditioning (HVAC) system, necessary to maintain strict climate control. At Metec, we advocate for the use of advanced HVAC systems equipped with smart sensors and controls that optimise energy use by adjusting the conditions based on real-time data from the environment. These systems can dynamically regulate temperatures and airflow, significantly reducing energy consumption without affecting the facility's critical operations.
A key challenge is to ensure top-down air diffusion within a cleanroom, to ensure satisfactory velocities and distribution to allow the particles to remain buoyant in the air, so that they can be extracted through low level return grills and removed from the space entirely. This system usually consists of multiple AHUs serving fan filter units (FFUs) via distribution ductwork. The Fan Filters Units can incorporate a supply diffuser and potentially HEPA filters which are usually not hard connected to the branch ductwork above, which allows the HEPA filters to be removed for maintenance.
As noted above, the return grills are installed at low level within the rooms to ensure laminar airflow and to assist in particle removal, to maintain the pressure differential between the Clean room and surrounding rooms, and enhanced temperature stratification management.
This differs from the traditional method of ventilating a building which usually consists of an AHU externally, hard ducted to AC units which in turn serve supply diffusers within a ceiling void. The return grills are usually installed within the ceiling and can be left open to the ceiling void, where the AHU has a return duct left open within the ceiling or the grills can be hard ducted back to the AHU.
On a recent cleanroom project, we have 6 AHUs installed on the roof, delivering approx. 96m³/hr of tempered air to the space. We have utilised “free cooling” on the AHU’s. When the external air conditions are within a suitable range, the AHU’s damper will fully open to allow full fresh air to the space. The chilled water circuit serving the AHU’s is not operational at this time. This in turn, reduces the energy consumed by the AHU.
2. High-Efficiency Filtration Systems:
Implementing high-efficiency particulate air (HEPA) filters can drastically reduce energy usage. These filters are designed to trap contaminants while maintaining air flow at optimised levels, thereby preventing the HVAC system from overworking to maintain air quality standards.
Cleanrooms require high efficiency filtration systems designed to maintain extremely low levels of airborne particles and contaminants in a controlled setting. If small particles/contaminants were to circulate within the cleanroom, there is potential for these particles to compromise the quality of the product being produced.
By installing HEPA filters on the supply side of the ventilation system, this adds an additional level of filtration on the system and helps create laminar airflow within the cleanroom. It provides a constant supply of fresh air in a controlled and expected manner throughout the cleanroom, which in turn, prevents the recirculation of contaminants throughout the space.
On a recent project, the HEPAs have been installed on the local FFUs in lieu of the AHU to reduce the AHU units’ size and power consumption. Larger fans would have been required within the AHU to overcome the pressure drop associated with HEPA’s being installed in the AHU.
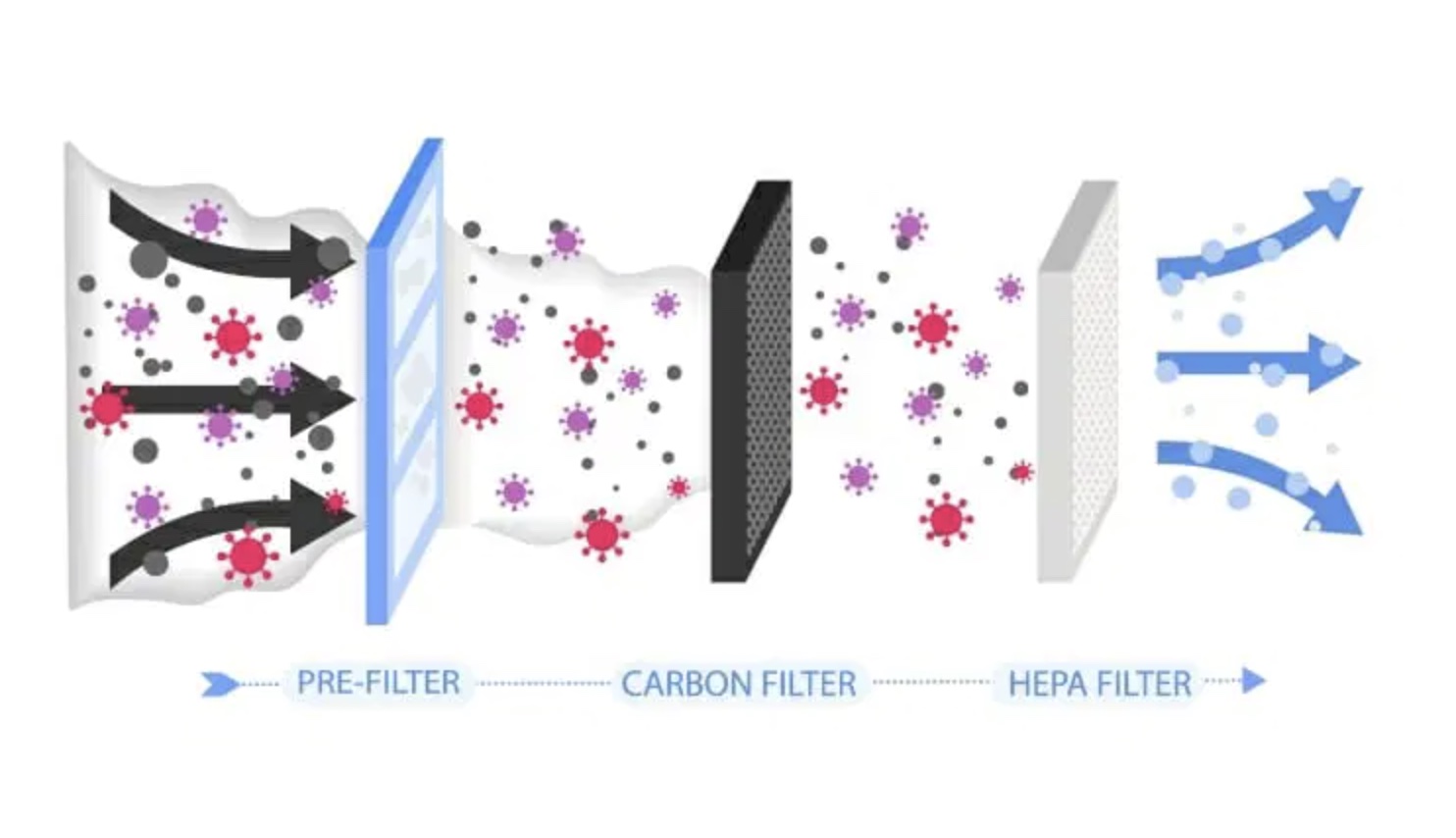
3. Energy Recovery Solutions
We specialise in integrating energy recovery ventilators (ERVs) that capture energy from exhaust air systems and reuse it to condition incoming fresh air. This method not only reduces the load on HVAC systems but also decreases the overall energy demand of the facility.
On a recent project, we also looked at utilising the waste heat from the compressed air system, as the primary heat source of the LTHW. The compressors, which have been specified by the process consultant, come complete with integrated plate heat exchangers and then connect into the LPHW central plant (Low loss header, buffer vessels etc).
Flow and return temperatures from the compressed air system were designed at 75 / 45 and feed the heating coils in the buffer vessels and hot water calorifier. Since the compressed air load is variable, the heat available for recovery is also variable. To assist in meeting the full LTHW load, a separate heat pump was installed on the return line of the process chilled water system.
By utilising ERV’s, we can precondition the air, by using the energy recovered from the cleanroom exhaust air. This reduces the energy required to either heat or cool the air to the cleanrooms and leads to substantial energy savings on the AHU, where strict temperature or humidity control is required.
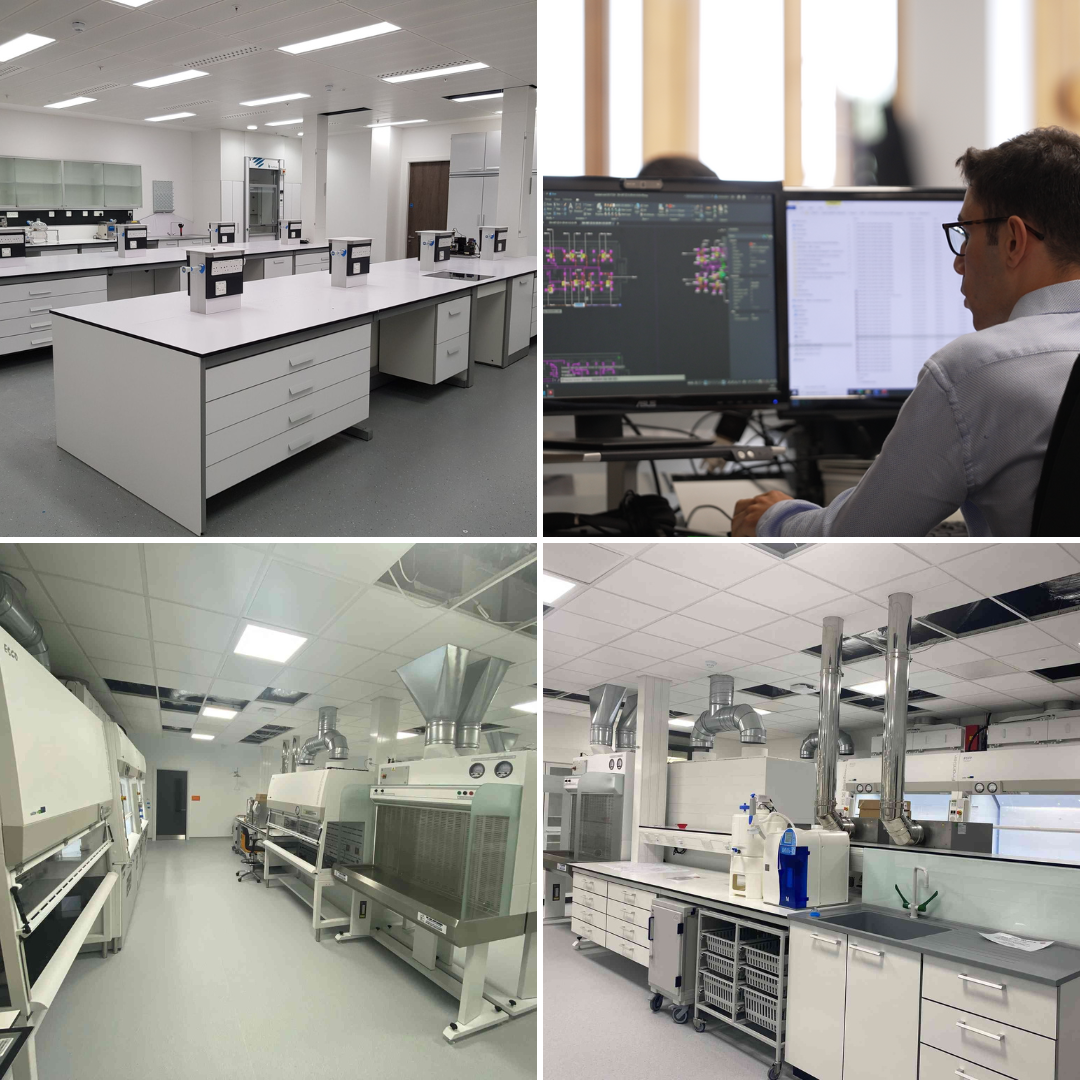
4. Building Automation Systems (BAS)
Implementing BAS to manage and monitor mechanical and electrical equipment in facilities can lead to significant energy savings. These systems provide centralised control of the environment, lighting, and HVAC, improving energy efficiency and reducing manual errors. There are usually 3 main control points in relation to Life sciences. These include the below:
- Temperature Control: Cleanrooms are designed to maintain tight temperature control (+-2°C) in order to ensure integrity of the product.
- Humidity Control: Cleanrooms are designed to maintain tight humidity control (Typically 40 to 60%, depending on the classification of the cleanroom) which is essential in preventing the growth of microorganisms.
- Pressure Differential between Zones: This is essential in preventing cross-contamination between adjacent rooms. Different zones in the building will have varying pressure requirements. For example, cleanrooms usually have a positive pressure differential, compared to adjacent rooms to keep contaminants out of the cleanroom.
On one of our recent projects, a Qualified Building Management System (QBMS) has been installed. This system controls conditions in critical areas such as a clean room environment. This allows for the control of plant and equipment such i.e. AHU’s, energy metering of LTHW and CHW and connection to the fire alarm, in order to shut down plant / equipment in the event of a fire.
The BAS will also inform the Facilities Management (FM) company of any failures of a component within the system. This allows the FM team to quickly diagnose the issue and action efficiently. Most critical systems are designed with a backup in mind (N+1) so that if one piece of equipment fails, i.e. a pump, the BAS can quickly isolate and shut down pump 1 and quickly engage pump 2 to start up and run, therefore, there is no downtime in HVAC systems serving the life science building.
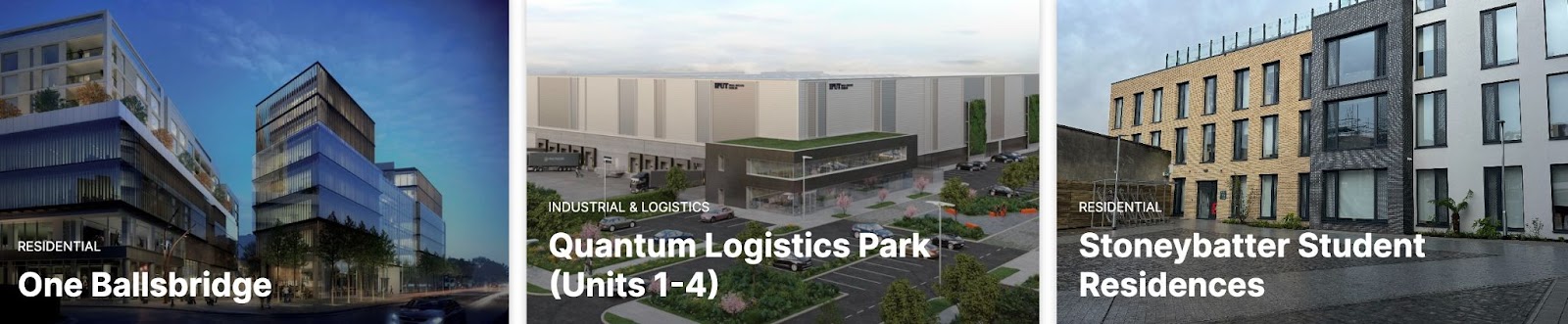
5. Sustainable Building Design:
At Metec, we emphasise the importance of sustainable building design from the ground up. Utilising modern architectural strategies such as orientation, shading, and thermal mass can naturally reduce energy needs before mechanical systems even come into play.
The orientation of the building can play a crucial role in reducing the energy consumption of a building. By orienting the building so that it maximises the natural daylight, this will in turn reduce the requirement for artificial lighting within the building. Daylight sensors can be installed so that the lux level varies, based on the level of natural daylight within the space.
External shading can help reduce the solar gain. Incorporating shading such as brise soleil onto a façade of a building can help obstruct / reduce the solar gain from entering the building and therefore reduce the cooling load on the air conditioning systems.
By utilising low emissivity windows on the facade, this can help reduce the solar gain into the space and therefore reduce the cooling load on the air conditioning systems.
Careful selection of the thermal mass can help to maintain stable internal temperatures. Materials used in the building fabric can absorb heat during the day and release it when the temperatures are cooler. This in turn helps reduce the load on the air conditioning system.
In colder climate areas, the location of the thermal mass is critical and can be positioned so that the solar gain heats the mass up, and when the internal temperature starts to drop, the thermal mass can release this heat into the space and reduce the heating load on the air conditioning system/heat emitters.
Natural ventilation can be utilised with careful design of the openable section of windows, which allows for fresh air within the space and therefore reducing the ventilation requirements of the AHU’s / HRU’s.
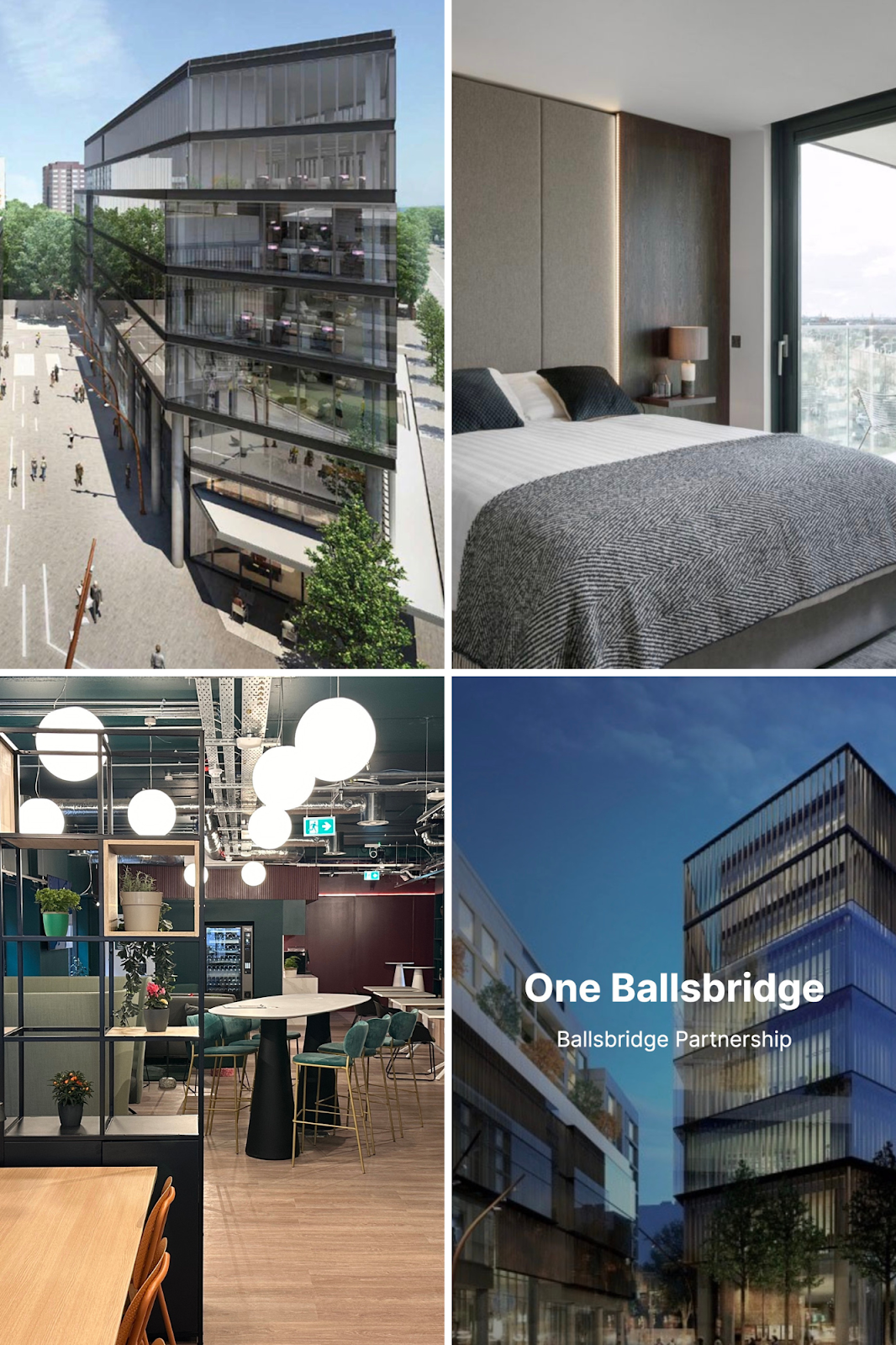
6. LED Lighting Systems:
Switching to LED lighting which consumes less power and lasts longer than traditional lighting solutions can drastically reduce the electricity demands of a life sciences facility.
LED lighting is more efficient and uses less energy than the traditional incandescent bulbs and fluorescent lighting while maintaining the same lumen level. LED lighting also produces less heat than traditional lighting and therefore helps to reduce the cooling load within the space and the associated load on the air conditioning systems.
LED lighting also allows for “dimming”, which utilises less energy and allows for greater control for the user of their environment. LEDs are able to maintain lumen quality and efficiency when dimmed, which traditional lighting technologies are not capable of.
The longer durability and lifespan of LED lighting also leads to fewer replacements of the LEDs and reduces the maintenance required.
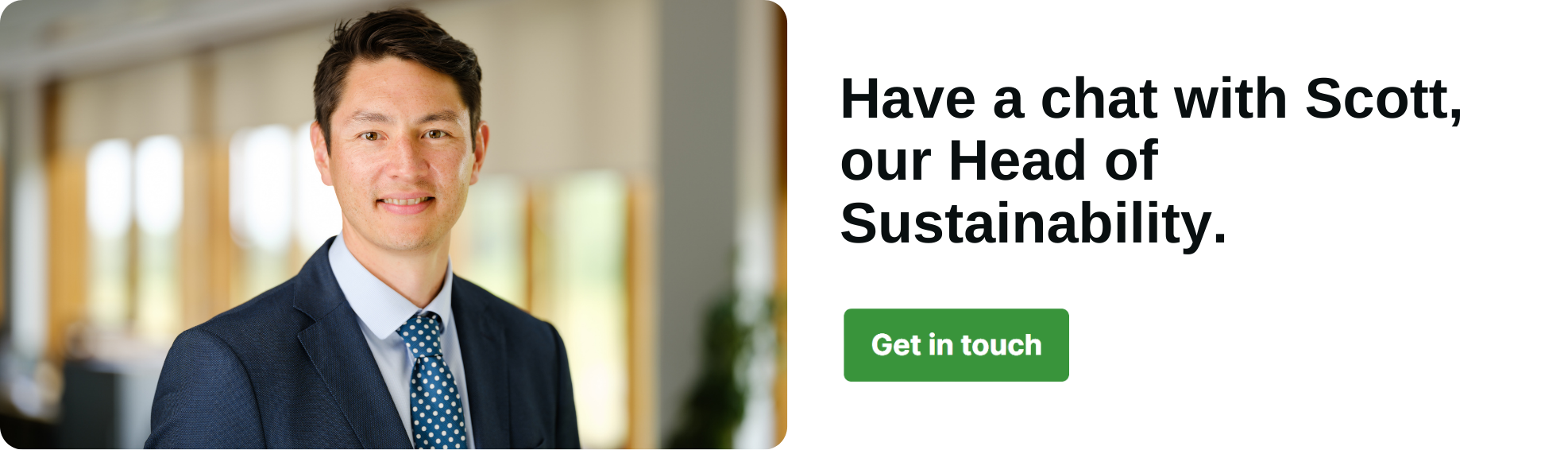
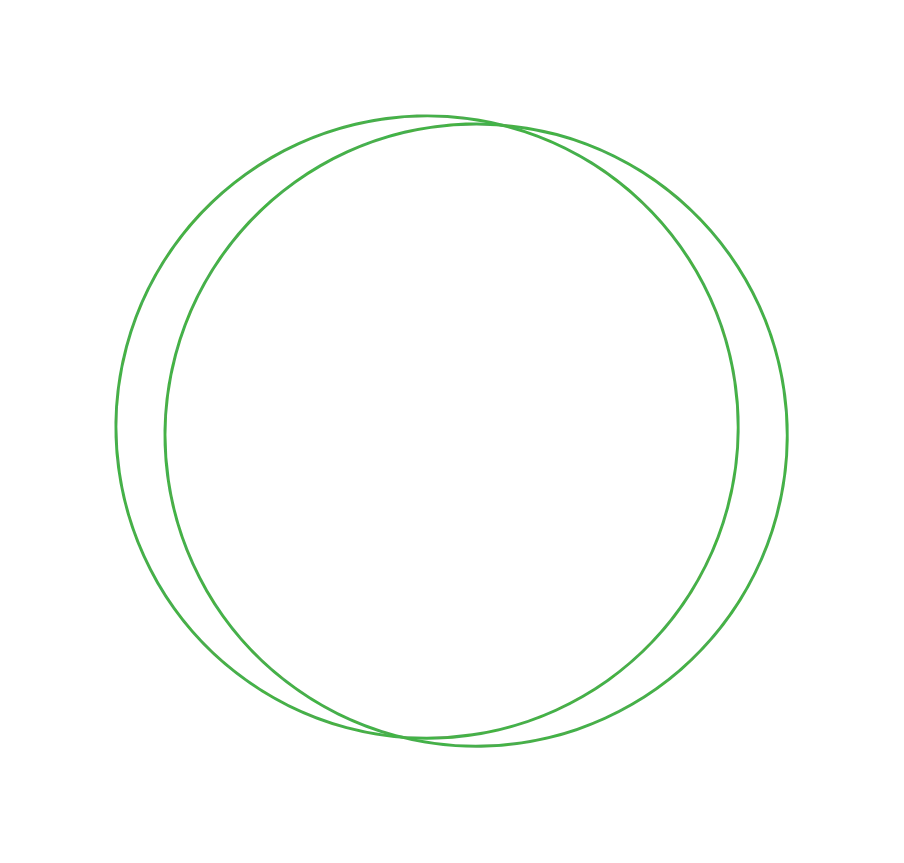
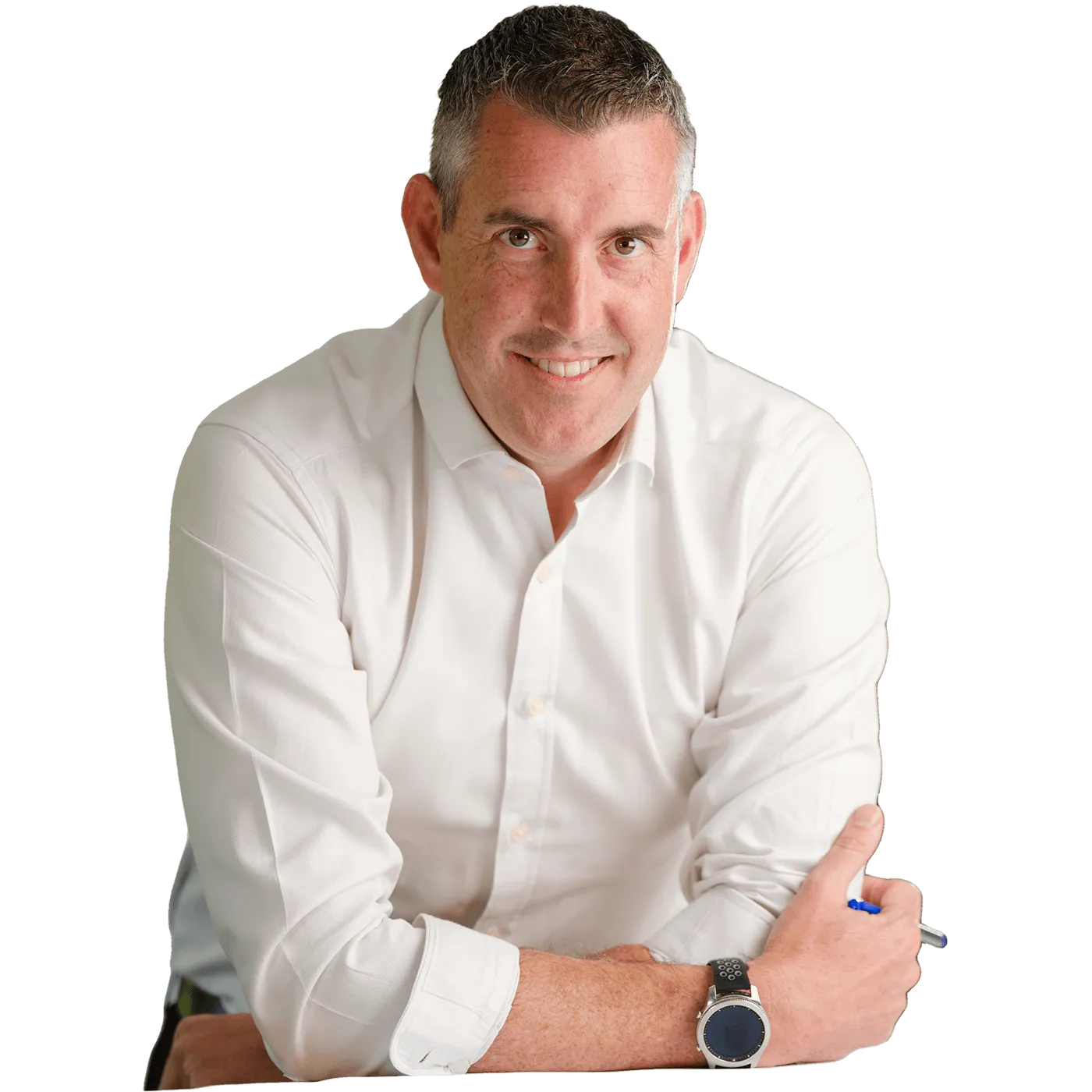